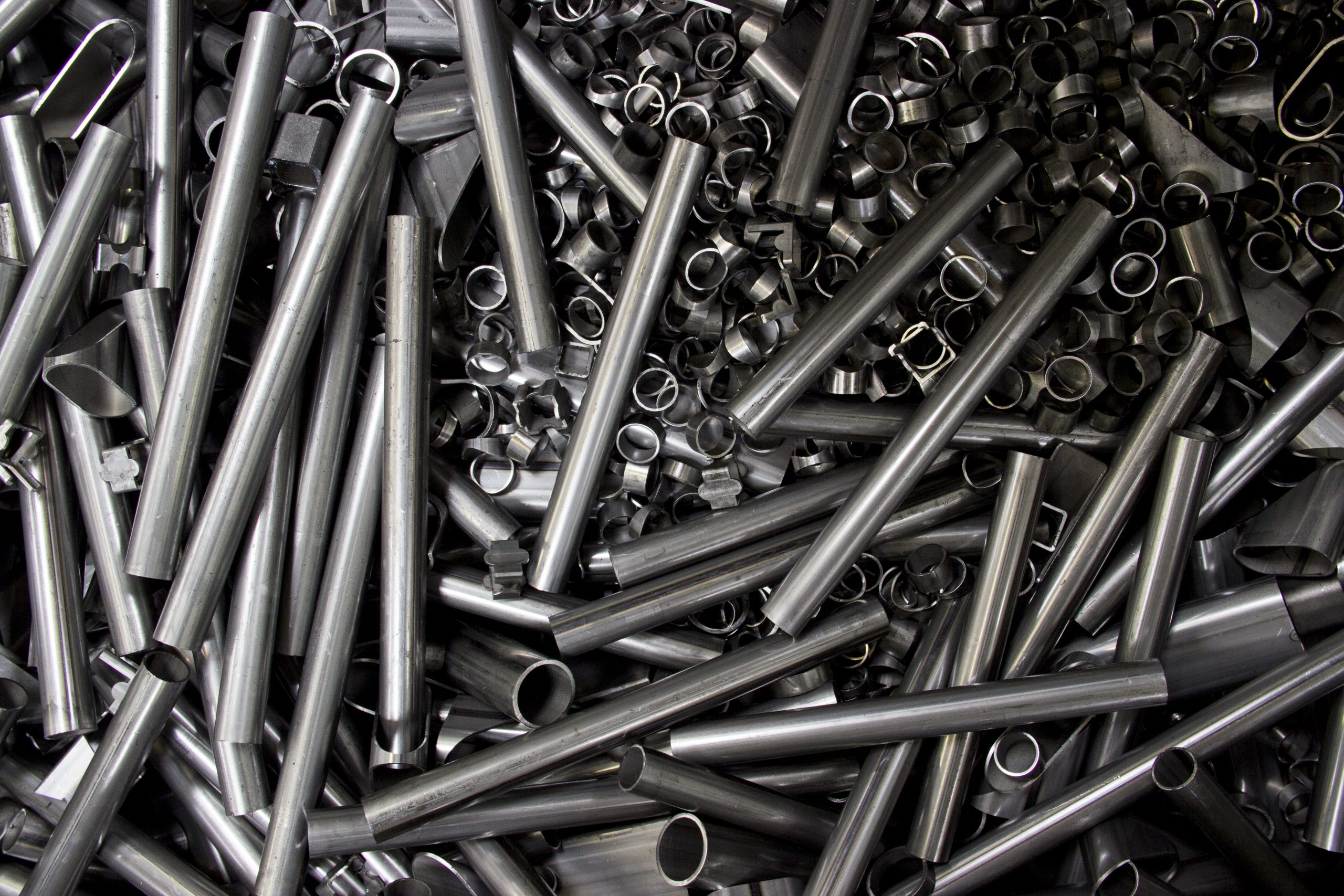
Made in Holland
Welkom in onze fabriek
Eromesmarko is trots om als een van de weinige meubelfabrikanten te kunnen zeggen dat al het eigen assortiment geheel in Nederland geproduceerd wordt. Zo weten we zeker dat al onze producten volgens de hoogste kwaliteitseisen en onder goede arbeidsomstandigheden worden geproduceerd. Ook zijn we trots op onze milieuvriendelijke productiefaciliteiten. Onze locatie in Wijchen, waar het stalen meubilair gemaakt wordt, is een van de schoonste fabrieken van Nederland. Maar boven alles zijn we trots op onze enthousiaste medewerkers, die hier iedere dag hard aan het werk zijn om het meest duurzame, kwalitatieve en mooie schoolmeubilair te maken. Daarom laten we hen graag aan het woord om te vertellen hoe hun afdeling werkt, zodat je een goed overzicht krijgt van het gehele proces, van staal tot stoel.
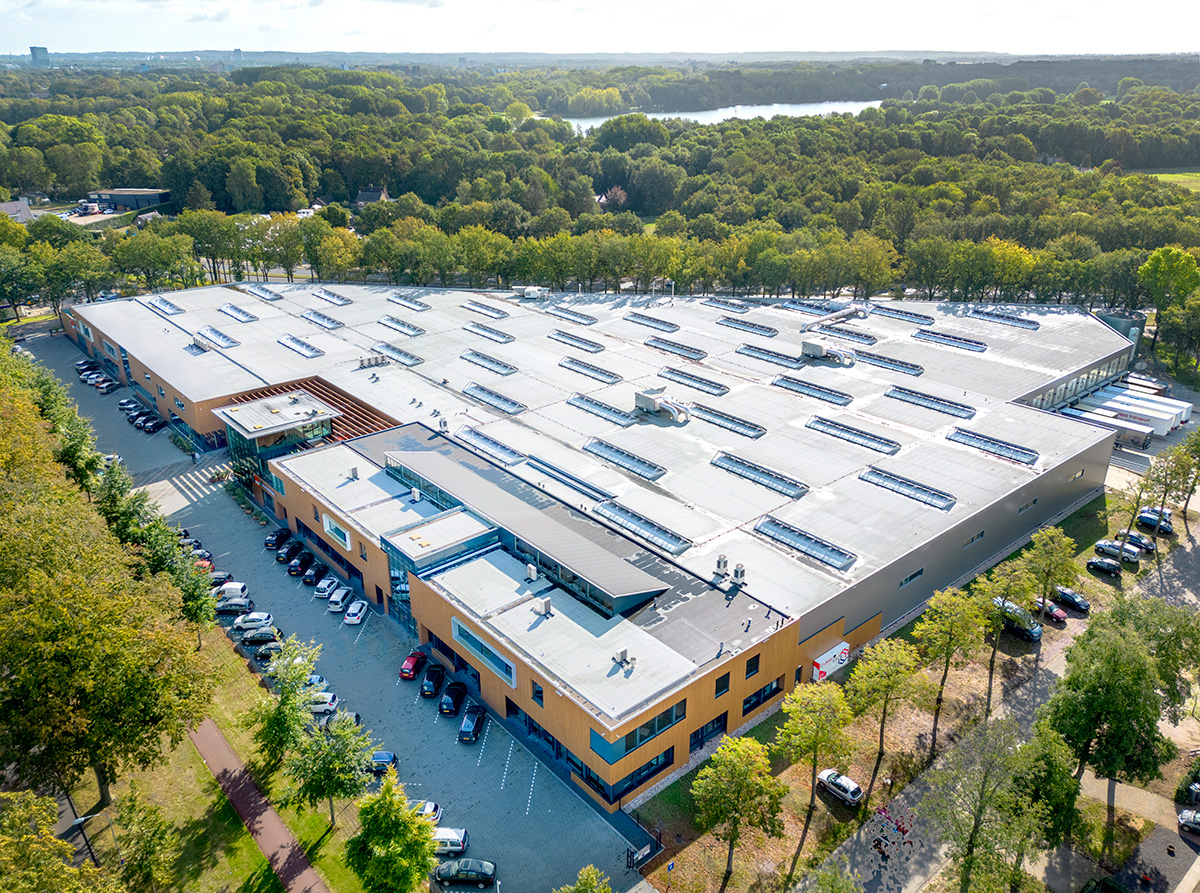
hulpvaardig
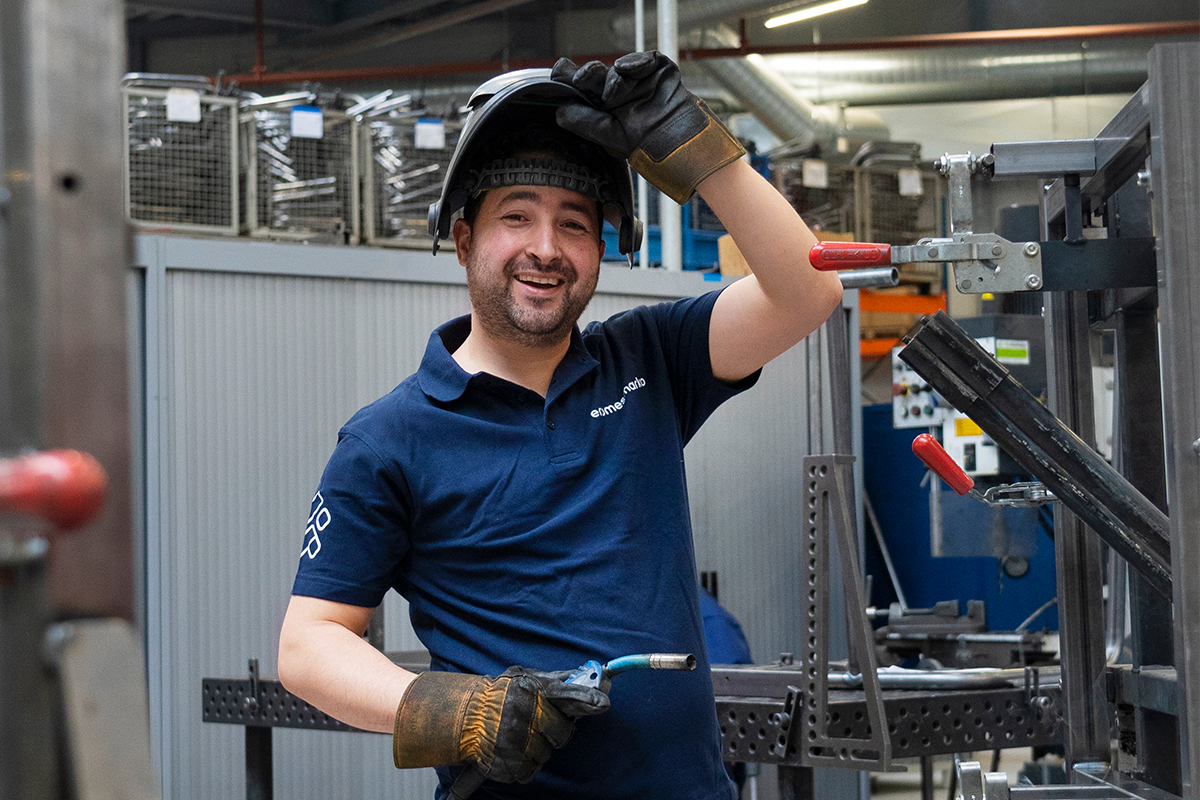
Van los staal tot frame
Metaal
Aan de ene kant van de productiehal komt het >30% gerecyclede staal van onze lokale leveranciers binnen voor de eerste verwerking: “Op de metaalafdeling vervaardigen wij complete gelaste frames, voornamelijk voor stoelen en tafels, uit de bundel ijzer die binnenkomt. We beginnen hierbij met het laseren van de onderdelen met onze lasermachine. Daarna gaan de onderdelen naar ons uitgebreide halffabricatenmagazijn óf naar de buigerij, waar de onderdelen in de juiste vorm worden gebogen met onze Veenstra en Wafios buigmachines. Alle apparatuur is CNC-gestuurd, wat betekent dat ze nauwkeurig worden aangestuurd door een gespecialiseerd computersysteem. De Wafios-machines zijn daarnaast uitgerust met een cameraherkenningssysteem. Ten slotte lassen we de frames af op een van de vier OTC MAG-lasrobots, onze Panasonic TIG/MAG-lasrobot of met de hand. Overige werkzaamheden die we uitvoeren zijn zagen, boren/tappen en ponsen.”
De monorail
Spuiterij
Alle nieuwe gelaste frames én de te revitaliseren retourgenomen frames gaan vervolgens naar de spuiterij: “We werken niet alleen binnen de afdeling nauw samen, maar ook tussen de afdelingen. Wanneer de metaalafdeling doorgeeft dat nieuwe producten gefabriceerd zijn, worden deze door een runner gesorteerd opgeslagen in een bufferzone. Van hieruit worden ze aan de hand van de dagplanning van onze teamleider klaargezet voor de spuiterij. We werken met een volwaardig poedercoatsysteem in combinatie met een monorail die zorgt voor een continu doorlopend proces. De frames worden hieraan bevestigd door een ophangteam dat bestaat uit een hakeneur, die controleert of de juiste producten klaarstaan en de bijbehorende haken aan de bewegende rail hangt, en een ophanger die de producten ophangt en de ruimte opgeruimd houdt.”
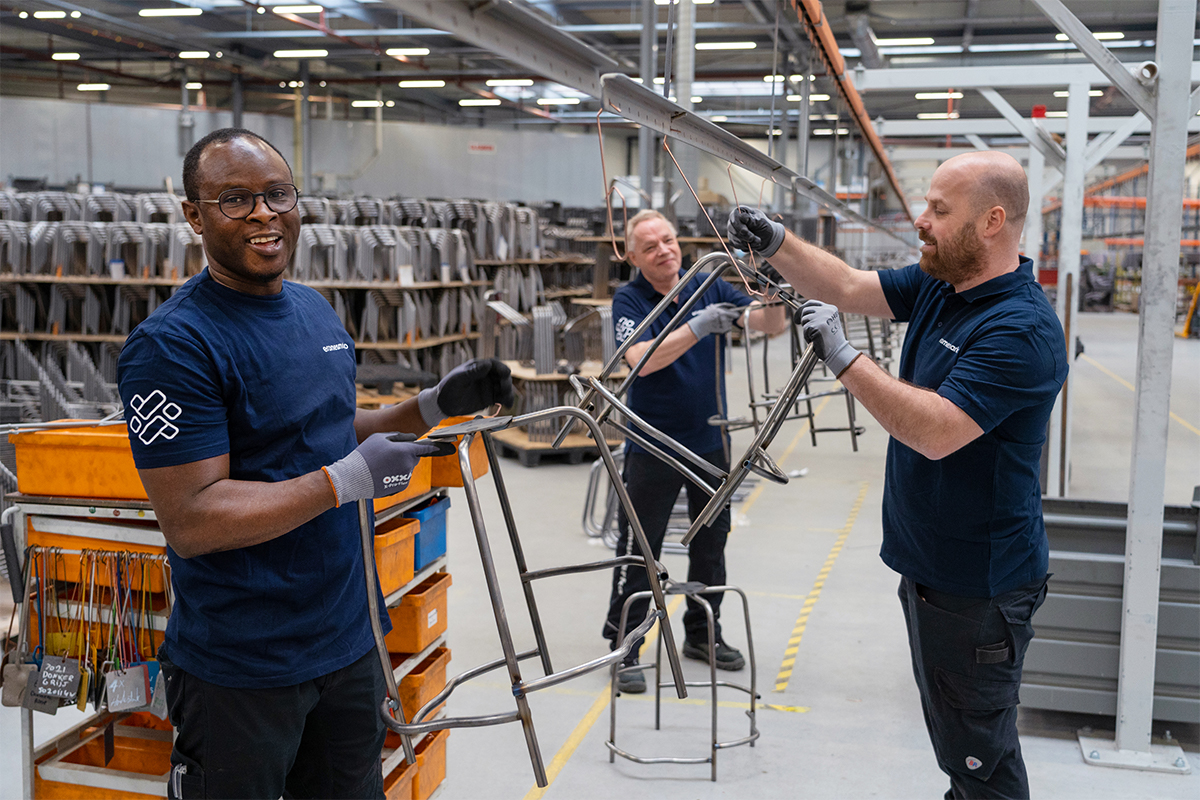
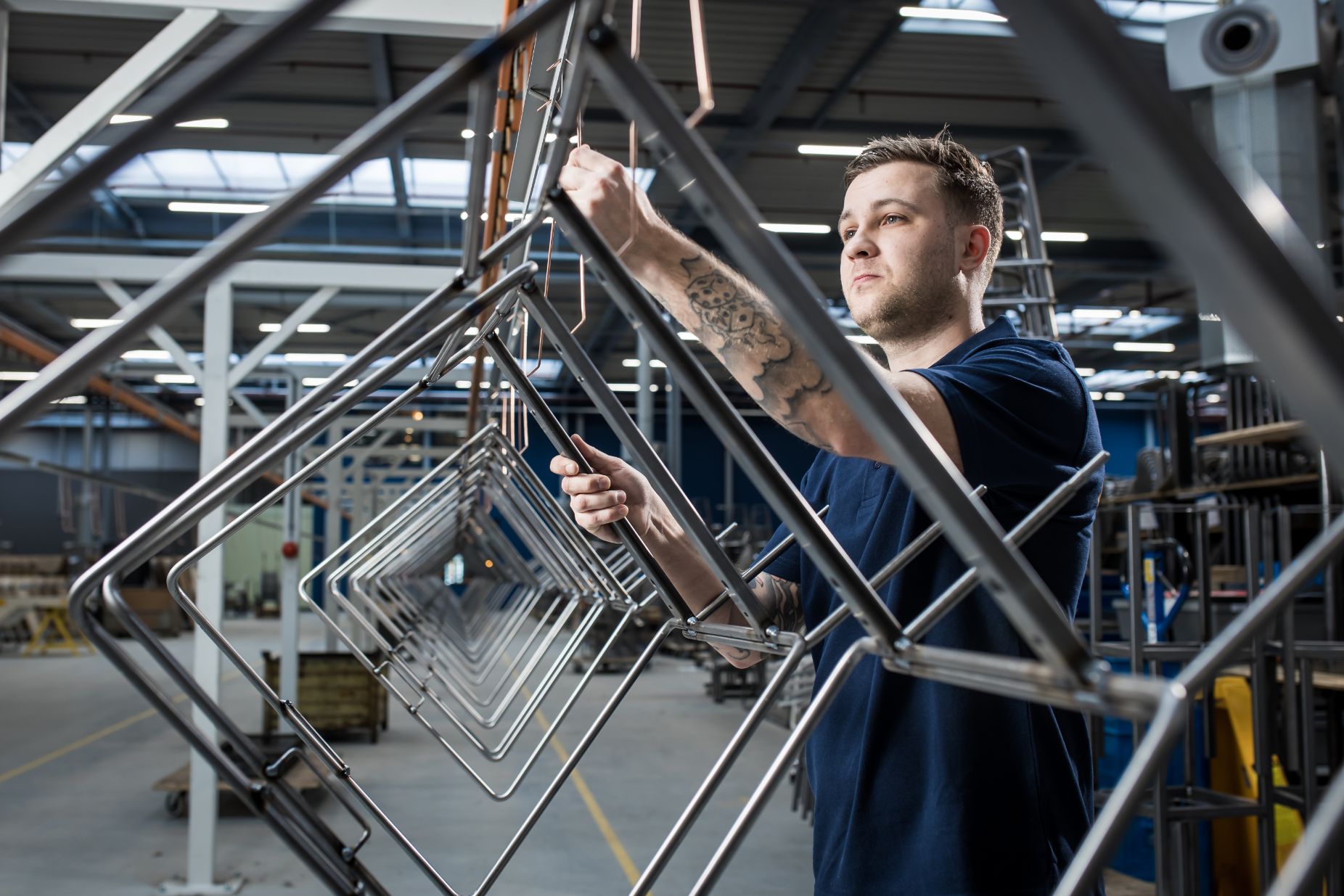
De spuitcabine
Spuiterij
Dan begint het daadwerkelijke poedercoaten; een schone en efficiënte technologie die bovendien een goede prijs/kwaliteitverhouding geeft. “Nadat de producten voorbewerkt zijn en door de droogoven zijn gegaan, komen ze aan bij de spuitcabine met een spuitrobot. Een spuiter is verantwoordelijk voor het bijwerken van plekken die voor de robot lastig te bereiken zijn. Daarnaast maakt hij meerdere keren per dag de spuitcabine en het poederstation schoon, wanneer er van poederkleur gewisseld wordt. Hiervoor is veel ervaring nodig, want als verschillende poedercoatings met elkaar vermengd raken is dat direct terug te zien in het eindresultaat. Wanneer de producten zijn gespoten en uitgehard in de moffeloven komen ze aan bij de afhaler die de producten controleert, van de rail afhaalt en klaarzet voor de montageafdeling.”
Tafels en stoelen
Montage
“Voor zowel de leerlingstoelen als de leerlingtafels is er een gespecialiseerde montageband waaraan 6 tot 7 medewerkers werkzaam zijn. Tijdens de drukke periode zijn beide banden continu in gebruik met 7 werknemers. Één van deze medewerkers doet altijd dienst als runner, die alle onderdelen en andere benodigdheden (frames, ruggen, zittingen, kuipen, doppen, schroeven, etc.) klaarzet. Aan de montageband wordt de kuip altijd eerst op het frame gezet en voorzien van een identificatie-etiket. Dan worden de pootdoppen, adapters, kleursticker die de hoogtemaat aangeeft, voetensteunen en andere onderdelen toegevoegd. Ten slotte wordt de kuip op het frame geschroefd of de rug en zitting worden met popnagels vastgezet. De complete producten kunnen nu gestapeld, geseald en geëtiketteerd naar de expeditie.
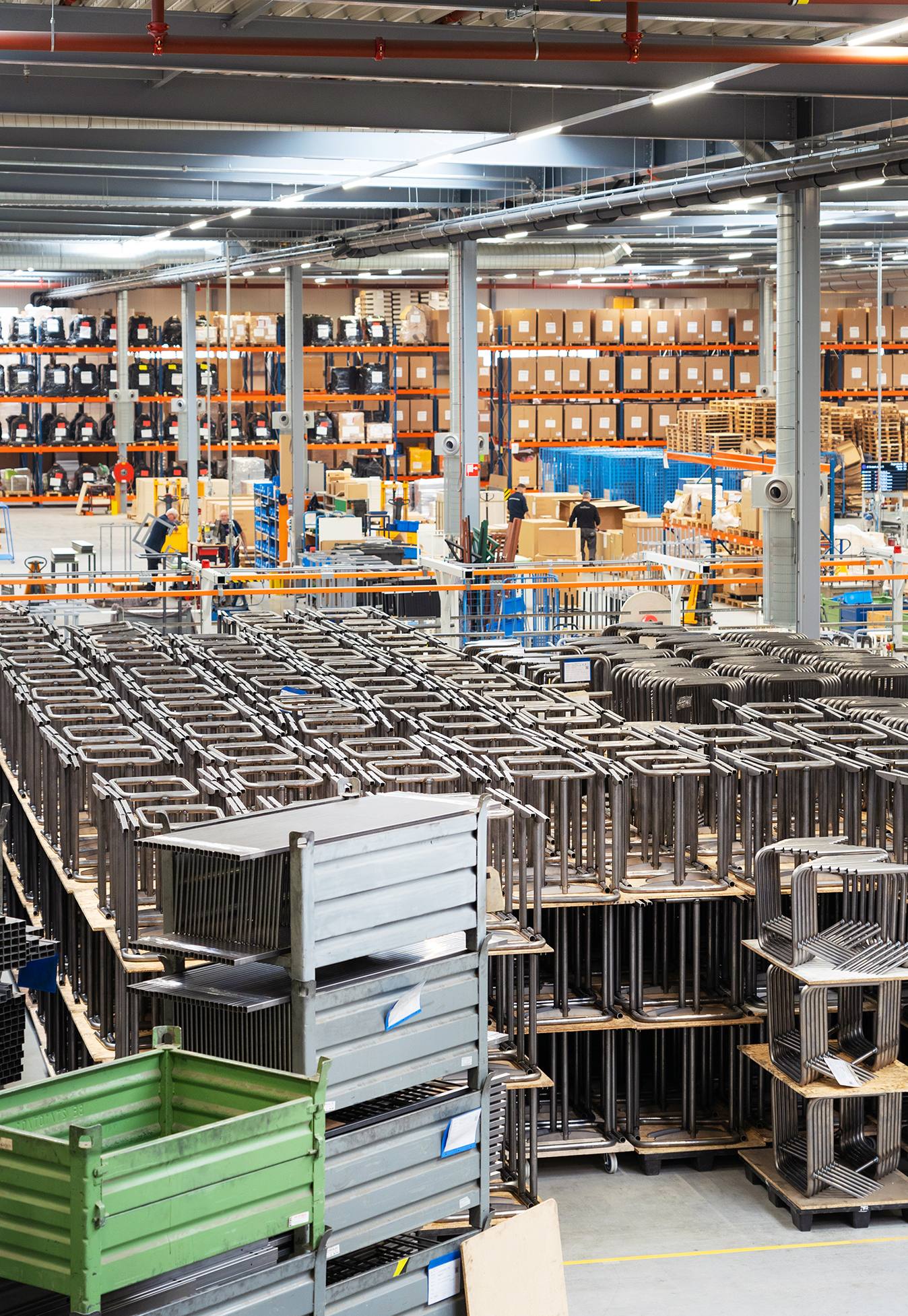
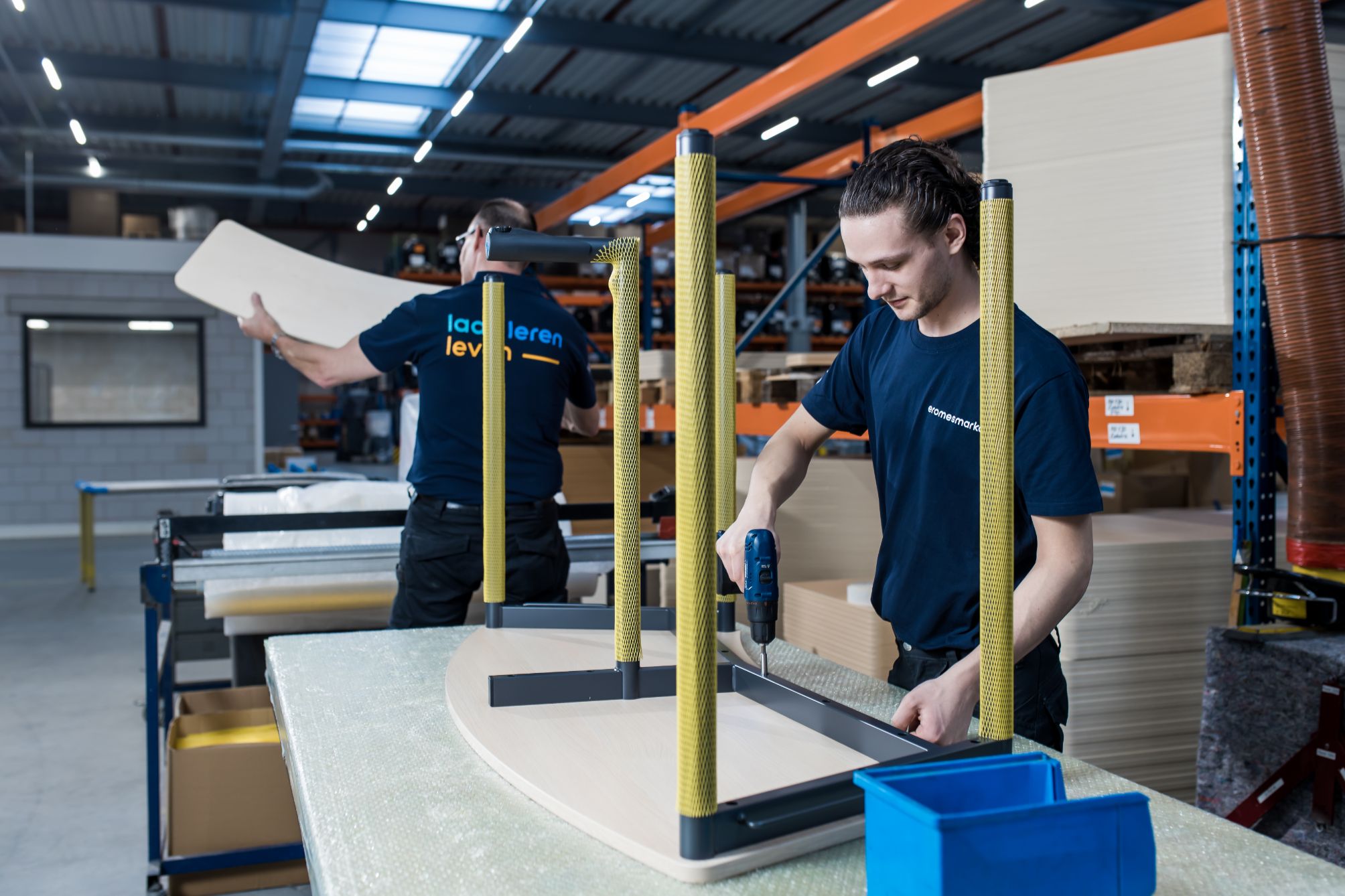
Overige producten
Montage
Alle producten die niet op de lopende band gemonteerd kunnen worden, gaan naar een aparte montageafdeling. “Op deze afdeling is iedere werkplek ingericht voor bepaalde producten. Hiervoor zijn er 3 afdelingen: de eerste is gespecialiseerd in grotere tafels en bureaus van de lijnen Luma, Dekring en Mix, de tweede is voor gestoffeerde (werk)stoelen zoals voor onze Seda Nova en afdeling 3 monteert allerlei overige productlijnen zoals Desq, Take a Break, Lola, Opta en Level. De houten bladen, metalen platen en stoffering komen van onze zusterbedrijven van de Fair Furniture Group, die deze fabriceren in Hoogeveen en Emmen. De monteurs zijn goed op elkaar afgestemd; bij grotere partijen werken ze in een doorlopend flow-proces waarbij de tacttijd (de tijd per handeling) wordt afgestemd op de grootte van het team.”
Van productie naar transport
Expeditie
“De compleet afgemonteerde producten worden op een pallet gestapeld, ingeseald of ingestrapt, voorzien van een partijetiket en beschermd met duurzame stoffen dekens in transportkarren geplaatst. Deze worden tijdelijk in een stelling opgeslagen die dienst doet als buffer, of rechtstreeks klaar gezet voor geplande vrachten. De artikelen worden zo efficiënt mogelijk in de vrachtwagens geladen om onnodige ritten te voorkomen, waarna onze eigen chauffeurs ze naar de klant brengen. De beschermings- en transportmaterialen en retourgenomen artikelen die zij direct mee terug vervoeren worden hier ook weer gelost. Verder zijn we verantwoordelijk voor het afhandelen van transportstromen tussen de verschillende productielocaties en het aansturen van de stroom restmaterialen, zodat deze duurzaam verwerkt kunnen worden en we hier afvalvrij kunnen produceren.”
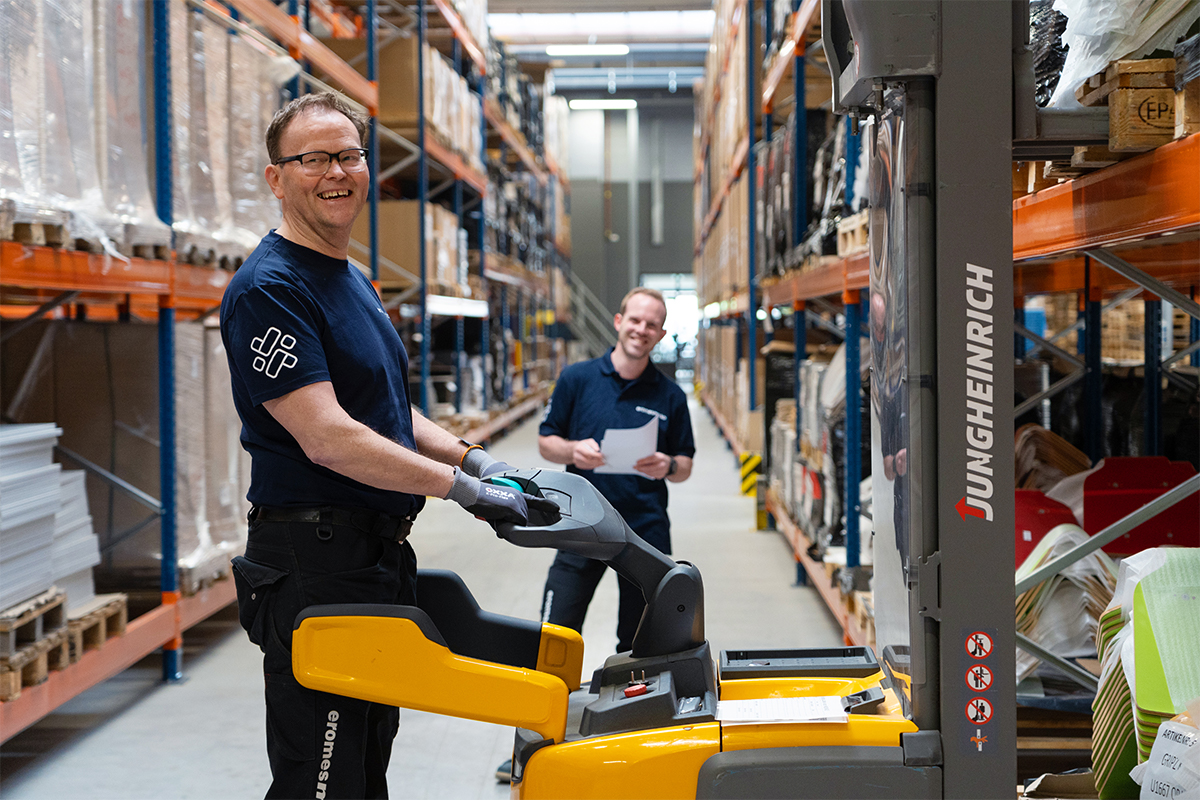